1. Why Rigid Plastic Packaging Bottles Require Leak Testing
Rigid plastic bottles are widely used in food, pharmaceutical, cosmetic, agrochemical, and beverage industries. Their sealing performance directly impacts product storage safety, transportation stability, and shelf life:
Issue | Detailed Description |
---|---|
Pharmaceutical bottle leaks | Active ingredient evaporation and moisture degradation |
Beverage bottle gas leakage | CO₂ loss affecting taste |
Lotion/essential oil bottle leaks | Label contamination and customer complaints |
Pesticide bottle sealing failure | Safety hazards and transportation non-compliance |
Poor bottle-cap fit | Increased IPQC/final inspection defect rates |
Therefore, pre-shipment bottle and cap seal integrity testing (leak testing) is critical for ensuring product stability, compliance, and market satisfaction.
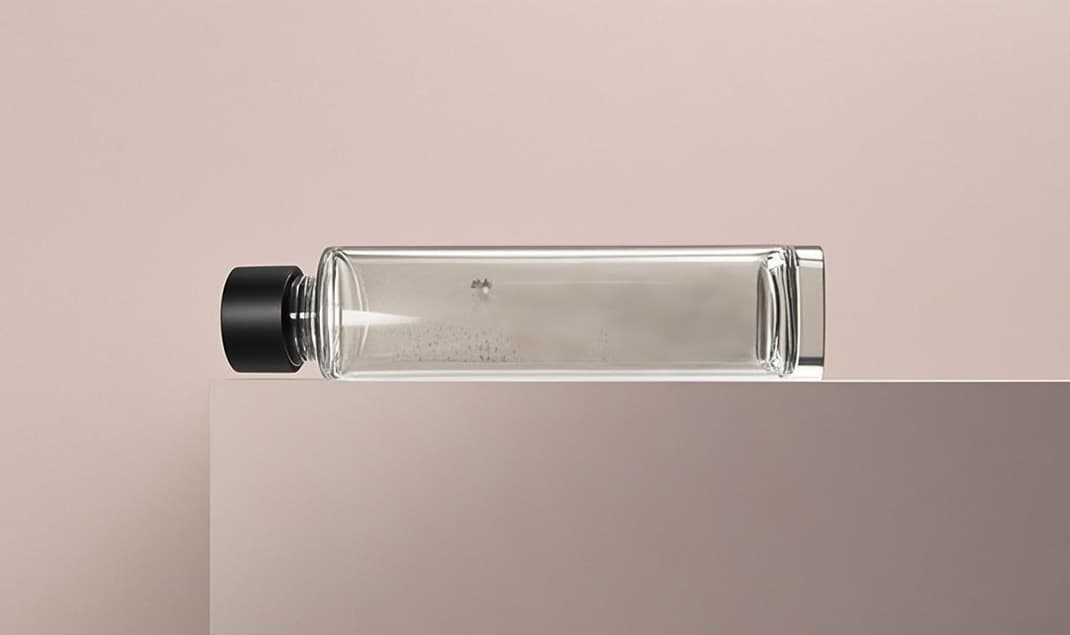
In 2023, a Zhejiang cosmetics company discovered leaks during transportation of shampoo products to Southeast Asia. Testing revealed incomplete cap threading causing minor leakage. The company implemented dual-channel leak testers (pressure decay method) for 100% online testing of bottle mouth seals, effectively resolving batch sealing issues and reducing after-sales complaints by over 70%.
2. Common Seal Integrity Testing Methods
Method No. | Method Name | Principle | Application | Notes |
---|---|---|---|---|
1 | Pressure Decay Method | Pressurizes bottle and monitors pressure drop over time | Common for empty or sealed bottle testing | Compatible with automated production lines |
2 | Mass Flow Method | Measures leakage rate (sccm) using flow sensors | High-precision requirements like medicine/essential oil bottles | |
3 | Vacuum Water Test (Destructive, sampling only) | Submerges bottle in water under vacuum to observe bubbles | Not suitable for production lines - lab testing only |
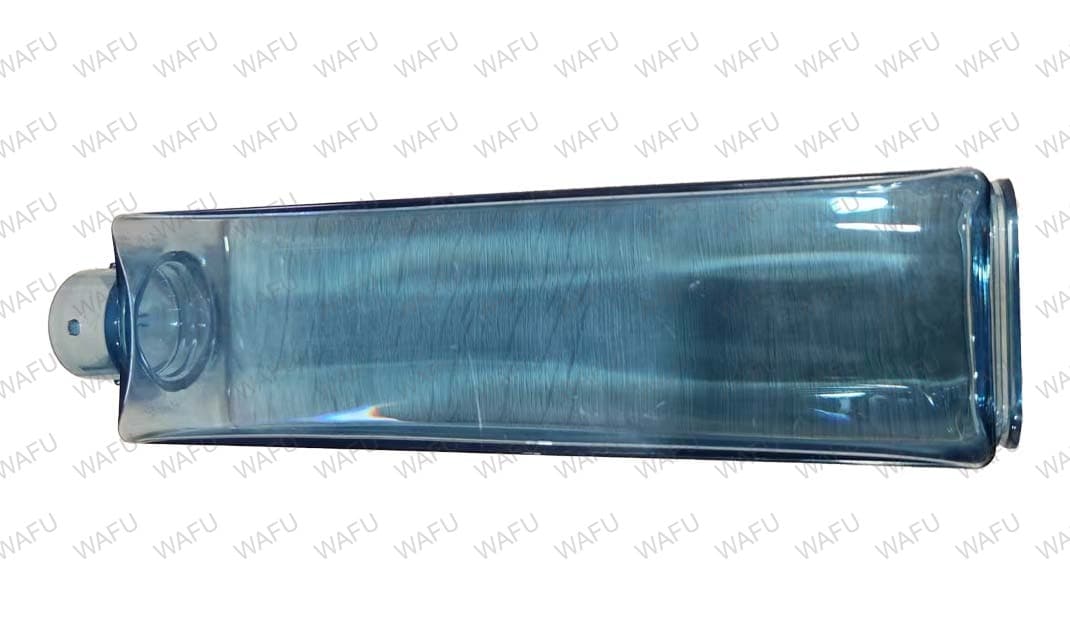
3. Standard Testing Procedure (Pressure Decay Method Example)
Step No. | Specific Procedure |
---|---|
1 | Bottle Fixturing: Place bottle in test fixture, sealing the mouth |
2 | Pressurization: Inject clean air/nitrogen to set pressure (e.g. 60kPa) |
3 | Pressure Stabilization: Maintain for 1-5 seconds, monitor pressure decay |
4 | Leak Judgment: NG if pressure drop exceeds threshold |
5 | Automatic Sorting: Separate pass/fail, compatible with MES traceability |
6 | Optional Cap Testing: Additional cap seal testing available |
4. Parameter Reference
Application | Test Pressure | Test Time | Pass Criteria (Leakage) |
---|---|---|---|
PET Beverage Bottles | 50 kPa | 5 s | ≤ 0.3 sccm |
HDPE Medicine Bottles | 80 kPa | 5 s | ≤ 0.2 sccm |
Essential Oil Bottles | 100 kPa | 10 s | ≤ 0.1 sccm |
Cosmetic/Care Product Bottles | 60 kPa | 3 s | ≤ 0.25 sccm |
The seal integrity of food composite film flexible packaging directly determines product shelf life, compliance, and consumer experience. Professional leak testing is essential for ensuring quality, safety, and compliant product release.
Recommended Products