1. Why is Leak Testing Necessary for Juicers?
As kitchen appliances, juicers often operate in humid and water-splashing environments. Inadequate sealing performance may lead to:
Issue | Detailed Description |
---|---|
Liquid penetration into motor/control chamber | Causing short circuits, electric leakage, or damage |
Failure to pass IPX4~IPX7 waterproof rating tests | Preventing market entry or export |
Liquid leakage contamination | Poor user experience and increased product complaints |
Higher leakage risk under high-pressure juice impact | Post-sale issues due to unverified sealing design |
Liquid leakage during transport due to pressure changes | Package contamination and increased return rates |
Therefore, conducting leak tests on complete units or critical components before leaving the factory is essential for ensuring safety, waterproofing, leak prevention, and compliance.
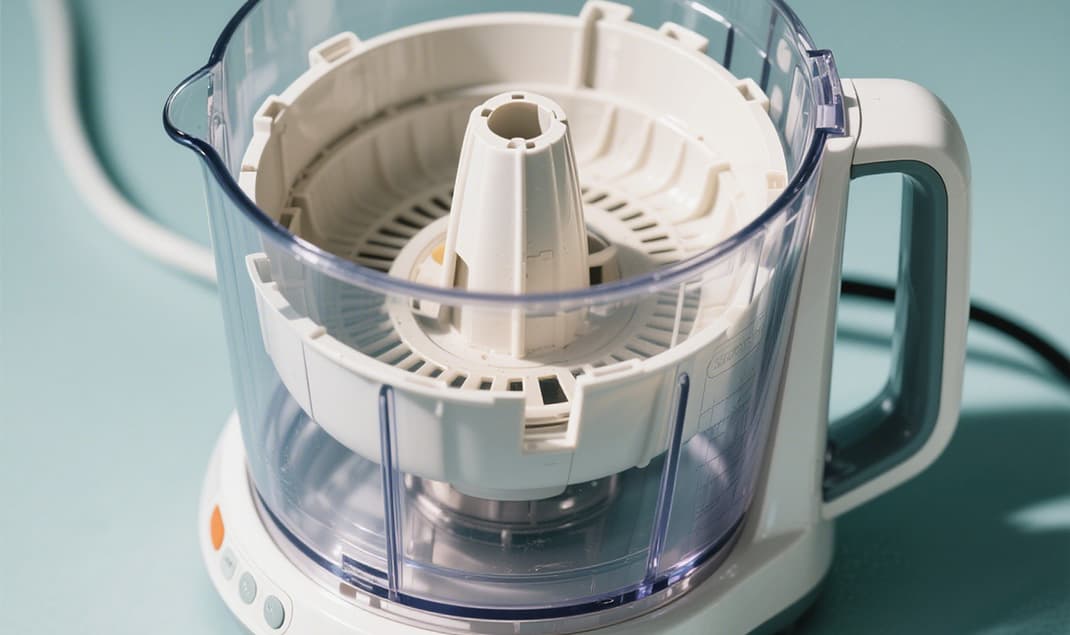
In 2022, a Guangdong-based juicer brand received complaints about leakage issues when listed on Amazon's European and American platforms. Inspection revealed improper assembly of bottom motor compartment seals in certain batches. The company implemented dual-channel leak testers (mass flow method) for 100% testing of motor chambers, setting a leakage standard ≤0.3 sccm. This effectively reduced defect rates below 0.5% and successfully passed European CE certification and IPX5 waterproof testing.
2. Suitable Methods for Juicer Leak Testing
Method No. | Method Name | Principle | Features |
---|---|---|---|
1 | Mass Flow Method | Real-time monitoring of gas leakage volume per unit time | High precision, fast response, suitable for complete unit or key component testing |
2 | Pressure Decay Method (Differential Pressure) | Detecting pressure drop to determine leaks | Suitable for component-level testing, such as juice outlet seals or cup body interfaces |
3 | Water Immersion Method (for R&D phase) | Submerging unit or parts in water and observing bubbles | Destructive, low efficiency, not suitable for mass production |
3. Recommended Testing Procedure (Using Mass Flow Method for Complete Units)
Step No. | Specific Procedure |
---|---|
1 | Fixture Installation: Mount juicer main body on testing fixture, sealing test area (e.g., motor chamber) |
2 | Pressurization: Set test pressure (e.g., 80~100kPa) and inject clean compressed gas |
3 | Stabilization Monitoring: Maintain constant pressure while monitoring leakage flow (unit: sccm) |
4 | Judgment Criteria: Determine pass/fail based on flow rate, output OK/NG signal |
5 | Automatic Recording: Save data to system for quality traceability |
The leak tightness of juicer products directly affects their waterproof rating, safety performance, and user satisfaction. Using leak testers for complete units and critical areas is a standard process to ensure product reliability, leak prevention, and waterproof compliance.
Recommended Products