1. Why is Leak Testing Essential for Integrated Control Valve Water Meters?
Integrated control valve water meters typically combine mechanical measurement modules, electric control valves, and communication modules, widely used in: smart remote meter reading systems, intelligent building/campus/industrial water management, supporting remote valve shut-off, automated meter reading and other functions.
Issue | Detailed Description |
---|---|
Moisture intrusion into electronic modules | Corrodes circuit boards, damaging communication or valve shut-off functions |
Micro-leaks in valve body | Prevents complete water shut-off, affecting meter reading and billing |
Seal aging/interface adhesive failure | Causes water leakage at user end, leading to accidents or complaints |
IP68 protection rating requirements | Mandatory leak testing + seal integrity verification before shipment |
Therefore, leak testers have become indispensable sealing quality control tools in smart water meter production lines, widely used in structural validation, full inspection before shipment, and IP certification support testing.
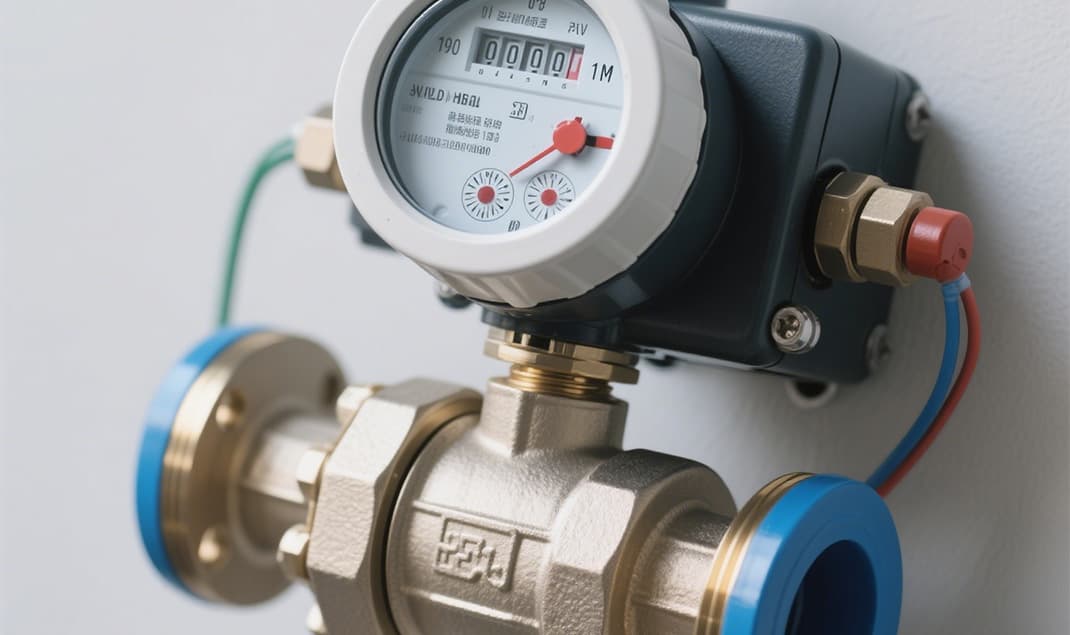
In 2023, a smart water meter manufacturer in Jiangsu needed to meet IP68 waterproof standards for "underground meter chambers" in southern China's water immersion environments. However, they failed third-party testing twice due to O-ring assembly deviations causing water seepage. After implementing high-precision leak testers (combining differential pressure and flow methods) for every unit's final inspection - with independent testing for valve bodies, control compartments, and water ports - their pass rate improved to 99.7%, enabling successful bulk bidding.
2. Common Air/Seal Tightness Testing Methods
Method ID | Method Name | Principle | Application Scenario | Characteristics |
---|---|---|---|---|
1 | Differential Pressure (Pressure Decay) | Detects leaks by monitoring pressure changes after pressurization | Ideal for sealed compartments, control chambers, and complete meter housings | Fast detection, suitable for production line integration |
2 | Mass Flow Method | Measures real-time leakage gas volume flow (sccm) | For high-grade seal verification like IP68 requirements | Provides precise quantitative leakage assessment |
3 | Vacuum Negative Pressure | Places meter in vacuum chamber to detect external air ingress | Suitable for backpressure testing in underground meter chambers | Can be combined with bubble immersion testing |
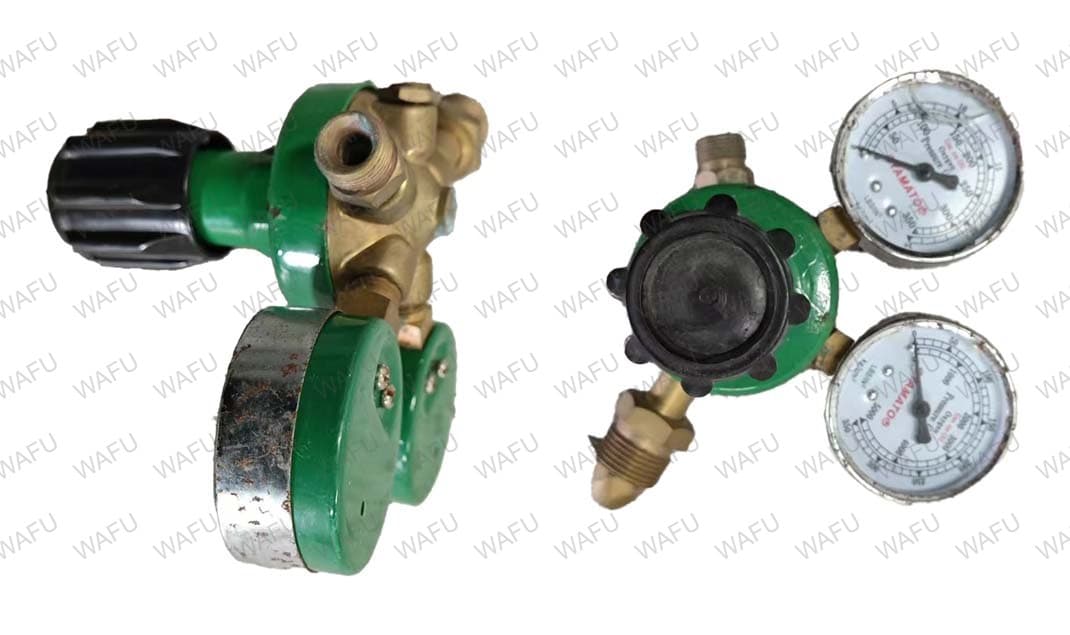
3. Typical Testing Areas and Process (Using Mass Flow Testing as Example)
Testing Area | Standard Testing Process |
---|---|
✅ Valve sealing chamber ✅ Communication module compartment ✅ Complete meter housing (including inlet/outlet ports) ✅ Vulnerable points: wiring ports, antenna ports, battery compartments |
Fixture setup: Mount meter in specialized test fixture, sealing water ports |
Pressurization: Charge internal chamber (e.g. 60-100kPa) for stabilization | |
Flow/pressure monitoring: Real-time leakage detection via tester | |
Pass/Fail determination: Automatic comparison against set standards | |
Data recording: Barcode tracking/automatic data logging with MES system integration |
Recommended Products