The Importance of the Airtightness of Mobile Phone/Tablet/Laptop Cases
In the consumer electronics industry, the case is not only a structural component but also the first line of defense against water resistance, dust protection, drop resistance, and liquid seepage. This is particularly critical in the following scenarios:
Requirements | Potential Risks |
---|---|
Mobile phones and tablets need to meet IP67/IP68 protection rating certifications; | If the seal is poor, it may lead to water entering the motherboard and battery → short circuits, corrosion, and failure; |
Laptops need to prevent liquid such as coffee and beverages from seeping in to ensure the safety of the motherboard; | Frequent dust and liquid entry during use → frequent brand complaints; |
Integrated metal structures require no gas leaks or incomplete seals at joints; | Failure to pass IP certification tests → unable to leave the factory, resulting in significant losses; |
The area where glass backshells and middle frames are combined needs to ensure even glue application and no micro-leaks. | Inability to advance to mass production during the trial production stage of new products → project delays. |
Therefore, using an airtightness tester for seal detection after shell assembly or before module encapsulation is a necessary step to ensure that the protection ratings meet the standards.
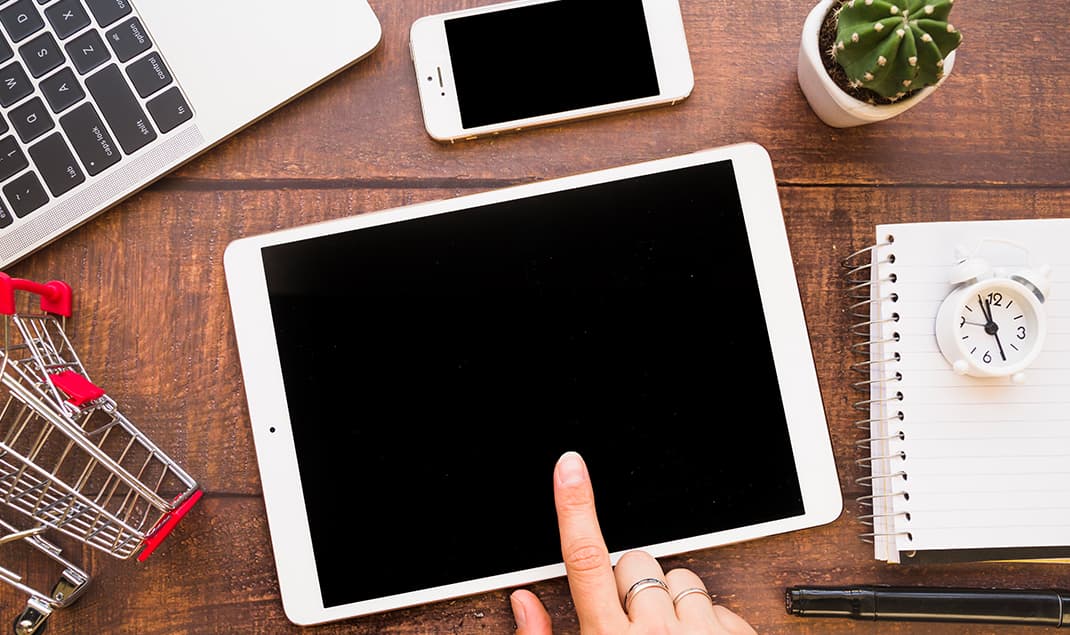
In 2023, a global consumer electronics brand introduced IP68 certification design for its new high-end series tablet. Initially, due to minor air holes at the middle frame bonding segment, some test units failed the pressure test and could not pass the high-pressure water spray certification. Ultimately, by introducing a high-sensitivity mass flow type airtightness tester, they conducted 100% seal detection and process iteration verification on the shell, successfully meeting the IP68 certification requirements and smoothly launching mass production.
For mobile phone/tablet/laptop cases, the following sealing detection technologies can be adopted:
Method Number | Method Name | Principle | Advantages |
---|---|---|---|
1 | Mass Flow Method | High precision, capable of detecting leaks at 0.1 sccm level; | Can be integrated into automated production lines for multi-position detection; |
2 | Differential Pressure Method (Pressure Drop Method) | Low cost, suitable for preliminary screening of structural components; | For complex structures or small test cavities, interference factors need to be controlled. |
3 | Helium Testing (Development and Verification Stage) | Used for micro-leak location in shell and confirmation of material micro-hole issues; | Used in conjunction with vacuum chambers or probe methods. |
Four, Detection Process (Taking Mass Flow Method as an Example)
Step Number | Specific Steps |
---|---|
1 | Fix the shell: Place the outer shell into a custom sealing fixture to simulate the post-assembly condition; |
2 | Seal Tightening: Use a cylinder to press the fixture, forming a closed test chamber; |
3 | Pressurized Inflation: Inject a clean gas source (such as air or nitrogen) into the test chamber, pressurizing it to a set value (such as 60~150 kPa); |
4 | Stable Pressure Detection: Maintain the pressure, and the system monitors changes in flow rate; |
5 | Leakage Judgment: Read the leakage flow rate value, if it exceeds the threshold (such as >0.3 sccm), it is judged as NG; |
6 | Automatic Output Results: Automatic sorting of qualified/unqualified items, uploading to MES system; |
7 | Data Traceability and Process Optimization: Trace anomalies, continuously improve in conjunction with shell manufacturing, gluing processes, etc. |
Airtightness testers are key equipment for ensuring waterproof performance in mobile phones, tablets, laptops, etc., and are also core supports for high-reliability delivery of entire machines and stable brand quality.