Lithium Polymer Batteries
Leak testers play a central role in the production and quality control of lithium polymer batteries (Li-Po), with their importance extending beyond product performance to directly impact battery safety, reliability, and compliance.
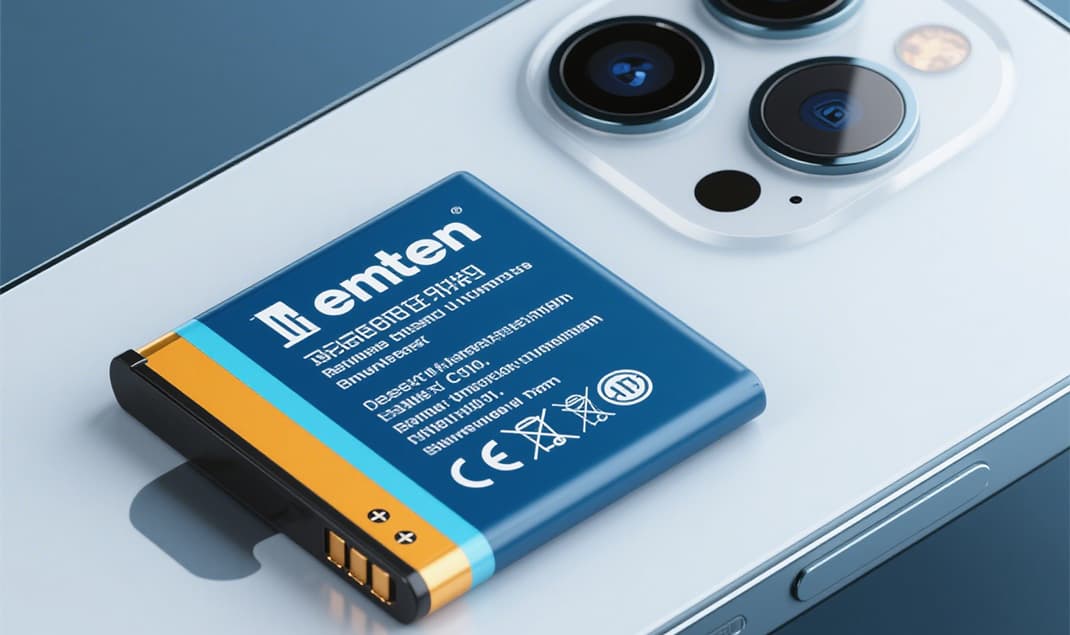
The core functions of leak testers in lithium polymer battery manufacturing include:
- Ensuring safety: Preventing electrolyte leakage and moisture ingress to avoid risks like swelling and combustion
- Enhancing quality: Maintaining stable battery capacity and longer lifespan while reducing after-sales issues
- Process control: Verifying whether sealing processes like heat sealing and welding meet standards to improve yield rates
- Meeting high standards: Complying with stringent sealing requirements for high-end applications like drones and medical devices
Below is a detailed professional testing solution:
Method | Pressure Range | Application Scenario | Advantage |
---|---|---|---|
Vacuum Method | -10~-20kPa | Standard mass production | Fast and cost-effective |
Positive Pressure Differential Method | 5~15kPa | High precision requirements (e.g., power batteries) | Accuracy up to 0.01mL/min |
Helium Mass Spectrometry | Vacuum environment | Laboratory-level verification | Detection limit 10⁻⁷ Pa·m³/s |
Typical Testing Process Demonstration
Phase | Specific Steps |
---|---|
Pre-treatment | Stabilize batteries at 25±2°C (temperature-controlled room) |
Scan and bind serial numbers | |
Testing Phase | Positive pressure mode: Inflate → Stabilize for 5s → Test for 10s |
Judgment standard: ΔP≤3Pa (equivalent to 0.03mL/min) | |
Post-treatment | Automatically sort NG products to helium retest station |
Upload data to MES (generate CPK reports) |
Recommended Products