Why Should Food Soft Packaging Bags Be Leak Tested?
Food composite film soft packaging bags are widely used for: ready-to-eat meals, dried fruits, meat products, dairy products, frozen foods, vacuum packaging, gas packaging (nitrogen/CO2), retort pouches, etc.
If the packaging bags are not sealed properly, it will directly affect food safety, freshness, and shelf life:
Issue | Detailed Description |
---|---|
Bacteria/Oxygen Entry | Food spoilage, deterioration |
Gas Leakage | Vacuum failure, bag bulging, collapse |
Oil Seepage or Liquid Seepage | Appearance contamination, affecting sales |
Frequent Customer Complaints | Damaged brand reputation |
Sampling Inspection Failure | Unable to pass QS/HACCP standards or export inspections |
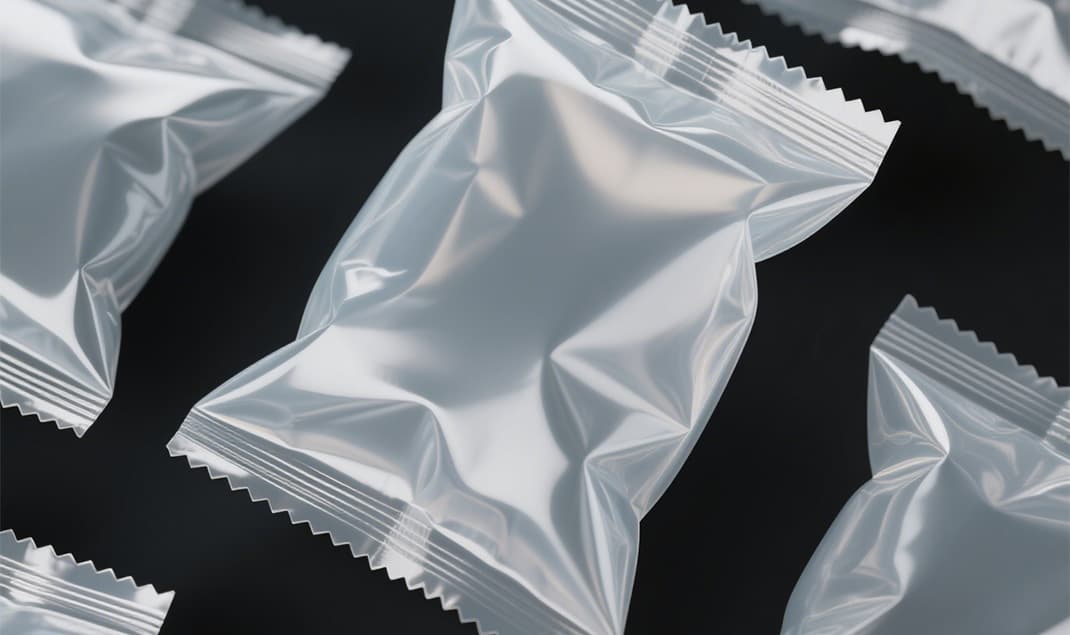
In 2023, a large food processing factory in Shandong exported a batch of high-temperature retort meat packaging bags, which experienced bag bulging and oil seepage during transportation. After investigation, it was found that part of the bag bodies were not sealed properly and had micro-leaks. The factory subsequently introduced leak detection equipment (negative pressure method + mass flow method) for sampling inspections, setting the standard as "negative pressure -30kPa, holding pressure for 60 seconds, leakage ≤ 5 sccm". The subsequent factory qualification rate significantly improved, successfully restoring stable export deliveries.
Common seal integrity testing methods for soft packaging bags:
Method Number | Method Name | Principle | Application Scenarios | Notes |
---|---|---|---|---|
1 | Vacuum Negative Pressure Method (Upgrade of Negative Pressure Sink Water Method) | By pressurizing or creating a vacuum to form a pressure difference, detect if the packaging bag is leaking. | Non-destructive testing, suitable for vacuum packaging, modified atmosphere packaging (MAP), etc. | Can be used with leak detection equipment to automatically determine if there is a leak. |
2 | Mass Flow Method | Detect the volume of leaked gas within a unit of time. | Can accurately determine the degree of leakage, suitable for sampling inspection or full inspection of high-end modified atmosphere packaging bags. | |
3 | Bubble Water Test Method (Traditional Method) | Submerge the packaging bag in water and pressurize to observe if bubbles emerge. | Destructive testing, suitable for laboratory sampling verification. | Not suitable for large-scale full inspection or automated production lines. |
4 | Seal Integrity Detection (Auxiliary Detection) | Used in conjunction with seal strength testers to detect the tensile strength of the seal, ensuring seal consistency. | Often used alongside leak detection. |
Four. Standard Testing Process (Using Vacuum Negative Pressure Method as an Example)
Step Number | Specific Steps |
---|---|
1 | Place in Detection Chamber: Place the sealed soft packaging bag into the sealed chamber. |
2 | Start Vacuuming: Set the vacuum pressure (e.g., -30kPa) and begin the vacuuming process. |
3 | Observe Changes: Maintain the pressure and observe if the packaging bag bulges, ruptures, or rebounds. |
4 | Leak Detection: Monitor pressure/flow changes in real-time using leak detection equipment. |
5 | Result Judgement: Bags with no bubbles or deformation are considered qualified, data is automatically recorded. |
6 | Output/Traceability: Inspection results are automatically sorted as OK/NG, uploaded to the MES system for traceability. |
The seal integrity of food composite film soft packaging bags directly determines the product's shelf life, compliance, and consumer experience. Using professional leak detection equipment for seal integrity testing is a key step in ensuring quality, safety, and qualified production.
Recommended Products